聯電導入工業4.0有成 南科廠整合AI演算法為每片晶圓規劃最佳傳送路徑
【記者蕭文康/台北報導】晶圓代工廠聯電(2303)宣布位於南科的Fab 12A廠入選世界經濟論壇(World Economic Forum)「全球燈塔工廠網絡」(Global Lighthouse Network),展現聯電運用工業4.0技術,提高生產力、效率及智慧製造成果。聯電Fab 12A廠不僅是聯電最大的生產與研發基地,更是全球首座榮獲燈塔工廠認證的半導體晶圓代工廠。
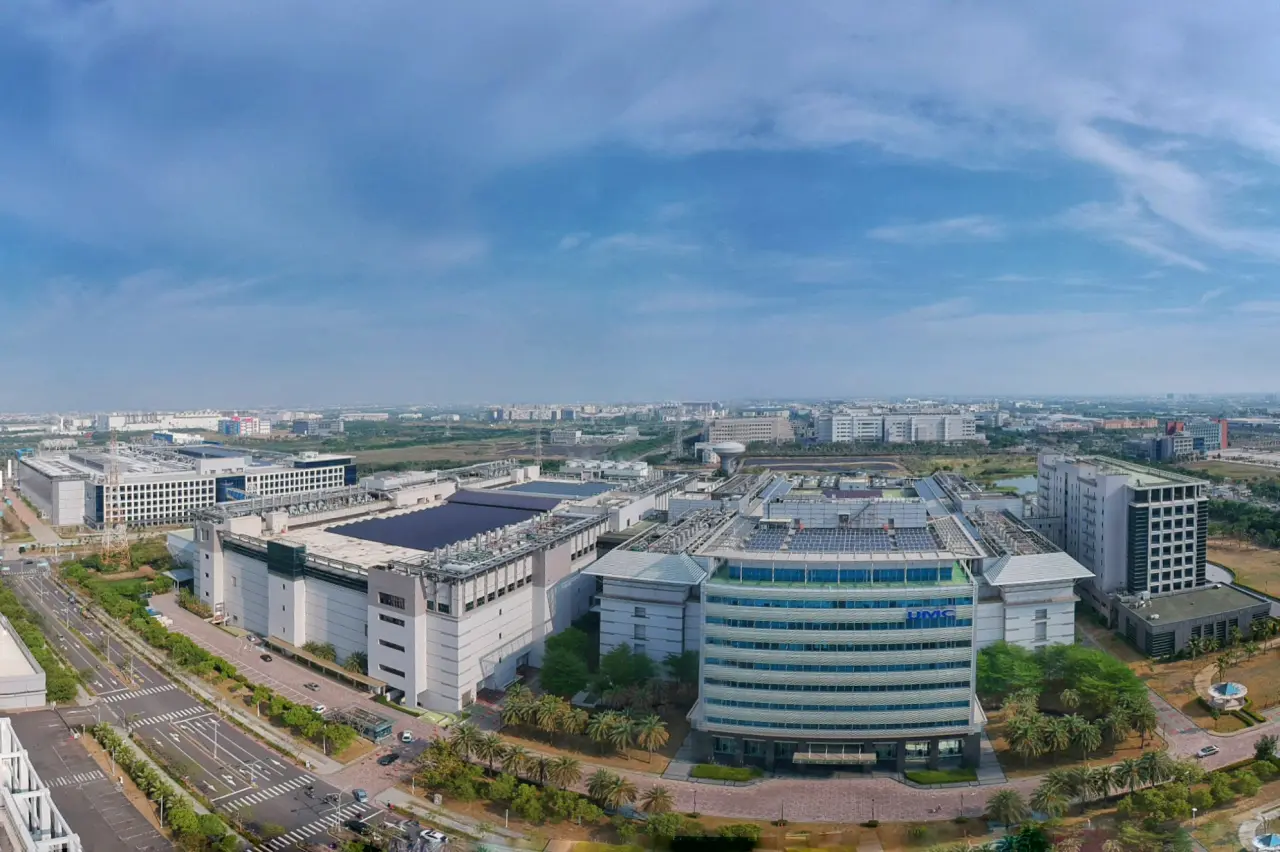
整合AI演算法和AMHS系統為每片晶圓規劃最佳傳送路徑
此次入選燈塔工廠的聯電Fab 12A廠是由三個獨立且相連的廠房組成,透過智慧自動物料傳送系統(Automated Material Handling System; AMHS)串連3000部機台和6800萬條可能的傳送路徑,將晶圓在跨廠區間進行自動化傳送。聯電整合AI演算法和AMHS系統,可自動為每片晶圓規劃出最佳的傳送路徑,全面提升工作和晶圓傳送的運輸效率。
全球燈塔工廠是由世界經濟論壇與麥肯錫公司於2018年共同提出,審查方式是由獨立的專家小組,評選出運用人工智慧(AI)、工業物聯網(IIoT)、大數據等技術提升效能與獲利的指標型工廠,評比範圍涵蓋30個國家和35個不同的產業,目前全球累積已有189座燈塔工廠。
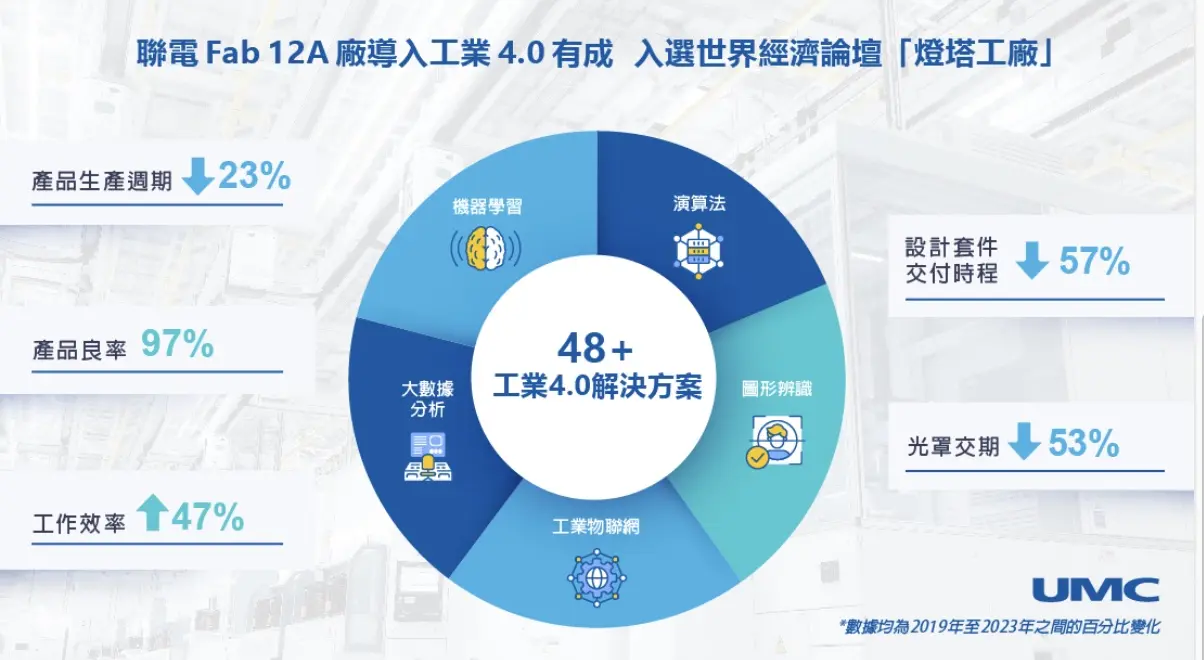
聯電2017年成立專責推動數位轉型的「智慧製造處」
聯電於2017年成立專責推動數位轉型的「智慧製造處」,率先以南科作為主要先導示範廠區,並逐步推展至其他生產據點。智慧製造處成立至今,透過將工業4.0技術整合到營運及上下游價值鏈,成功累積超過48件解決方案,其中近95%由聯電自主研發。透過這些解決方案,Fab 12A廠成功縮短57%的設計套件交付時程,提升產品良率至97%,同時增加47%的工作效率,進而提高客戶黏著度、整體製造效能與產品品質,對企業的營運及獲利做出貢獻。
聯電副總經理吳宗賢表示,很榮幸能夠獲得世界經濟論壇的認可,成為以大規模運用尖端技術於製造業的數位轉型先驅。聯電以工業4.0為永續發展的核心,確保聯電在日益競爭的市場中滿足客戶需求。智慧製造不僅可提升員工能力和工作效率,讓同仁專注於更有價值的工作,更在生產過程中優化各項資源使用上,降低對環境的衝擊。身為引領產業數位轉型標竿,聯電也將持續向其他在燈塔工廠網絡中的企業學習。
聯電強調,公司致力提供高價值的晶圓特殊製程解決方案,然而由於特殊製程對於規格的要求更趨於嚴格及精確,其複雜度也隨之提升。在工業4.0技術的助力之下,可有效應對特殊製程的複雜度及嚴苛標準,進而提升客戶的黏著度,讓聯電在激烈競爭的市場中脫穎而出,進一步提升企業的整體獲利能力。
聯電運用核心技術的導入和開發應用,推展出多方面的智慧製造專案。其中為了加速客戶產品的上市時程,運用機器學習工具,縮短設計套件交付時程一半以上。再來,為確保光罩的準確性和交付時間即時性,聯電開發了人工智慧平台,藉以精簡公司和客戶及供應商之間的資料處理流程。
此外,為了縮短產品生產週期,聯電針對製造過程中的瓶頸機台,採用「機器學習模型預測」和「智慧氣體切換系統」,縮短產品在生產過程中因氣體切換的調機與等待時間;同時也建立「智慧缺陷真因辨識系統」,結合智慧影像識別和自動化AI智能異常搜查比對系統,幫助工程師在極短時間內找出真因和造成缺陷異常的機台,有效提升產品良率。